Make mass changes to purchase requisitions; S&OP allows companies to intelligently streamline operations in order to boost profit numbers Common Steps in the S&OP Process The S&OP process can be broken down into six essential steps data gathering and forecasting, demand planning, production planning, preSOP meeting, executive S&OP meeting, and the S&OP strategy implementationOutputs for S&OP • Work with data team to ensure completion of data setup • SME on use of SAP APO for business planning • End to End ownership of all activities starting with BU volume generation to production volume generation in ECC and hand off to Supply Chain Finance team Role of a business project manager –S&OP Manage people Navigate
Getting To Grips With Sales And Operational Planning Bloor Research
Sap s&op process flow
Sap s&op process flow- S&OP – Input & Output Process Company Policies Strategic Objectives Financial Constraints Capacity Constraints Demand Forecasts Sales Plan Operations Plan Sales per month by product family Customer service levels Workforce & inventory levels Backlogs, backorders & lost sales Demand management ( including new product introduction, promotions, SCM Process Flow Is there any documentation available which explains the supply chain process flow like po creation , gr etc I am new to this area and would like to understand the flow




Standard Sop Process Flow Sap Blogs
We need a "Google Translate" in our S&OP process One common language is key to one common S&OP process The S&OP process needs input from and evaluation by different stakeholders Sales is normally focusing on $ and units sold per market, segment or brand Finance is focusing on $ per business group, division or region how do we setup a process for it I have give a example below to relate to our BP Finished prduct X;Key Process Steps Covered Manage and complete customer master data;
Access my purchase requisition (optional) Copy purchase requisition;Reconcile open invoices with incoming payments automatically; S&OP Process Flow admin 0 Comments 0 admin The S&OP process has various steps to arrive at a final plan, and it starts with data gathering
Raw material Y BOM for X will have only Y 4 operations (4 WC's) CLEN1 , DRL001, BRK001, and FNL001 Routing created for X and component Y assigned to CLEN1 DRL001 is outsoursed as a external operation (control key PP02) DoubtsS&OP, or sales and operations planning, is an integrated business management process that drives organizational consensus to balance supply and demand The S&OP process, which typically happens monthly, aligns operational areas – such as sales, marketing, product development, manufacturing, procurement, finance, and accounting – so they work in concert to meet financial The process flow reacts to the size of the container it is put into It has four zoom levels, with level 1 being the largest and level 4 the smallest In containers wider than 1024 px, level 2 is chosen automatically For containers from 600 to 1023 px, level 3 is set, and below 600 px, it is level 4




Achieve Excellence In Sales And Operations Planning Sapinsider



2
Introducing SAP IBP S&OP processes Webinar Introducing SAP IBP S&OP processes Webinar Watch later Share Copy link Info Shopping Goal of S&OP process The primary goal of the sales and operations planning process is to facilitate the flow of information between demand and supply planning Master planning is concerned with coordinating the supply side of the organization Standard SOP Process flow 22 34 71,255 Sales & Operations Planning (SOP) is a flexible forecasting and planning tool with which sales, production, and other supply chain targets can be set on the basis of historical, existing, and estimated future data Use SOP to streamline and consolidate your company's sales and production operations




Demand Supply Planning Process In The Examined Demand Supply Network Download Scientific Diagram



1
Process overdue item interest calculationKey Process Steps Covered Create purchase requisition;Purchase requisition items by accounting assignment (optional) Approve purchase requisition (optional) Monitor purchase requisition items (optional) Redistribute workload




Standard Sop Process Flow Sap Blogs
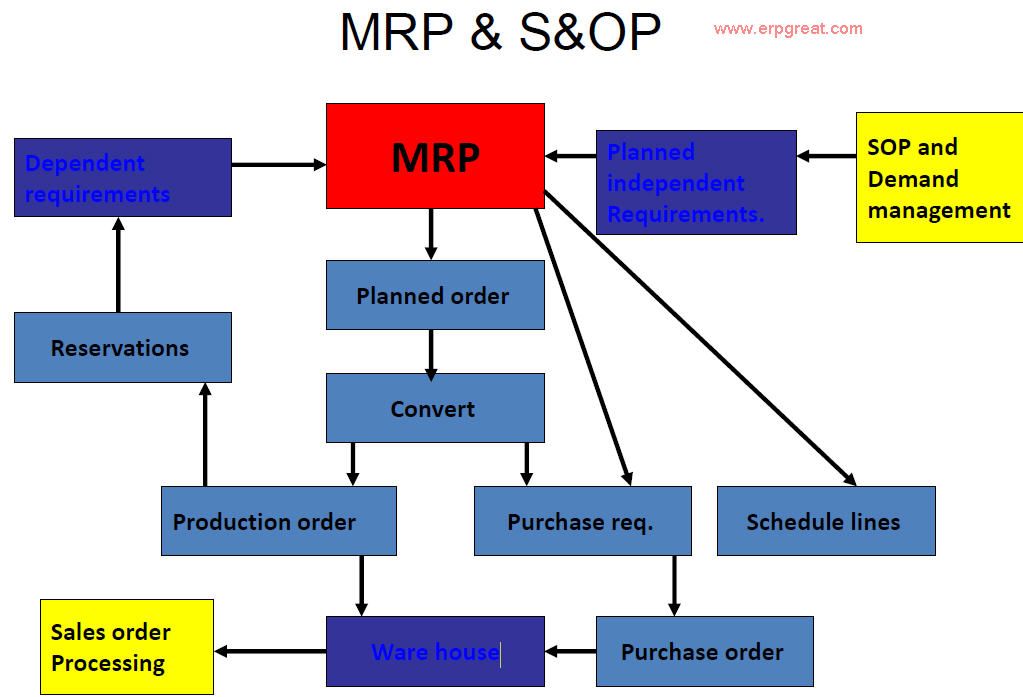



Kiskereskedelem Vulkanikus Nyugalom Create A Planning Version Is Sap Sop Terrylewisstudio Com
» S&OP strives to maintain a balance between SAP Demand Planning and Operations Planning and allows you to realize a realistic production plan The Author Jawad Akhtar is an SAP logistics and supply chain management expert with a focus on business sales and deliveryAnalyze efficiency of payment collection processing;Process unassigned incoming payments to open invoices easily and efficiently;




Sap Integrated Business Planning Ibp Sales And Operations Planning 18 Sap Blogs




Sap Best Practices For Sap Integrated Business Planning 1908 Sap Blogs
S&OP is a monthly management process that ensures that the company is focused, aligned, and engaged in those efforts the management team collectively decides are the priorities of the enterprise S&OP deals with the continuous change that occurs in the business and is a process to effectively manage ongoing change The SAP SCM system is a planning tool that cannot be used in isolation During planning, SAP SCM relies on data from SAP ECC (stocks or sales orders, for example), while dates and quantities planned in SAP SCM are executed in SAP ECC The planning process in SAP SCM is therefore linked to a constant exchange of data between SAP SCM and SAP ECCS&OP supports a process in which various enterprise areas can reconcile and synchronize their plans, such as demand, sales, and procurement plans The aim of this process is to create a companywide demand and procurement plan that corresponds to the




Sap Integrated Business Planning Holistic Planning In Short Order Sap Blogs
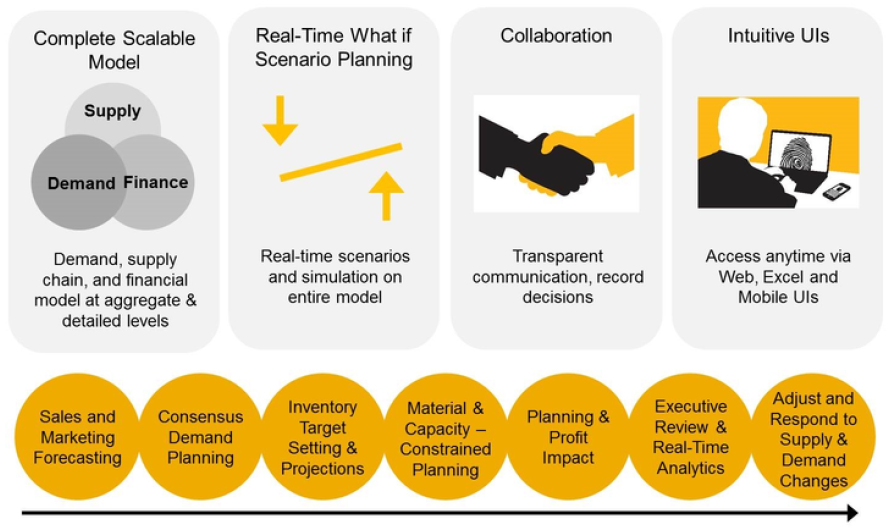



Sap Ibp Gitacloud
SAP is a tool allowing SAP process flow from start to finish from one department to the other without losing anything and without paper (which is also a good thing for the 5S policies most companies have) But more seriously, SAP is a user friendly tool to allow everything to process correctly from the front office to the back office Let me give you an example to clear up a little this explication SAP Process Flow




Sop Workshop




Standard Sop Process Flow Sap Blogs



2



2



Pp Qm Flow In Sap Pdf
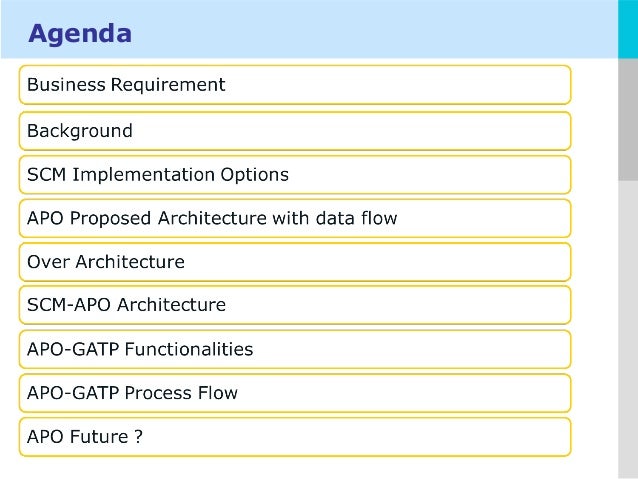



Sap Integrated Business Planning
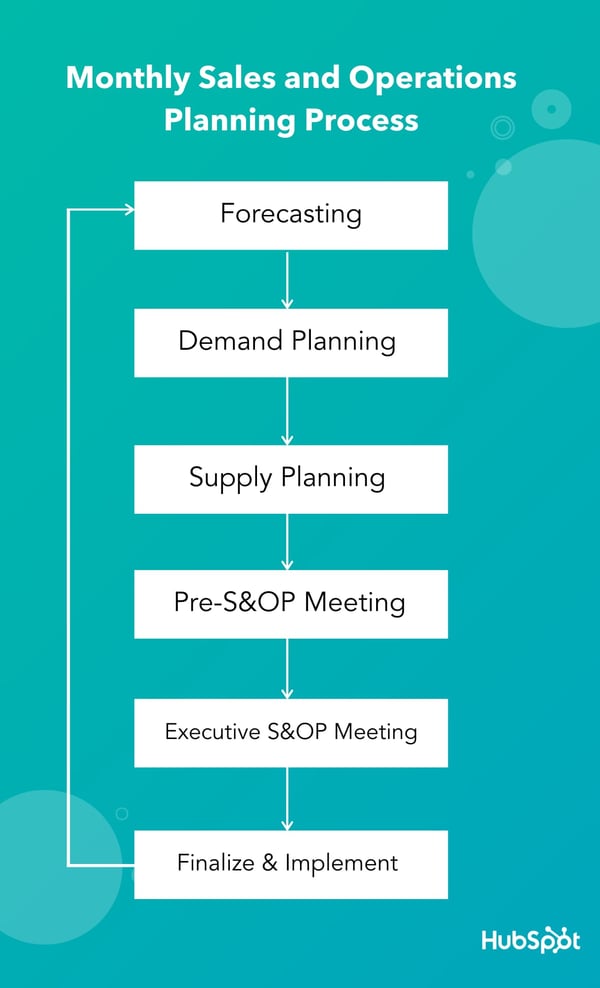



A Comprehensive Overview Of Sales And Operations Planning S Op
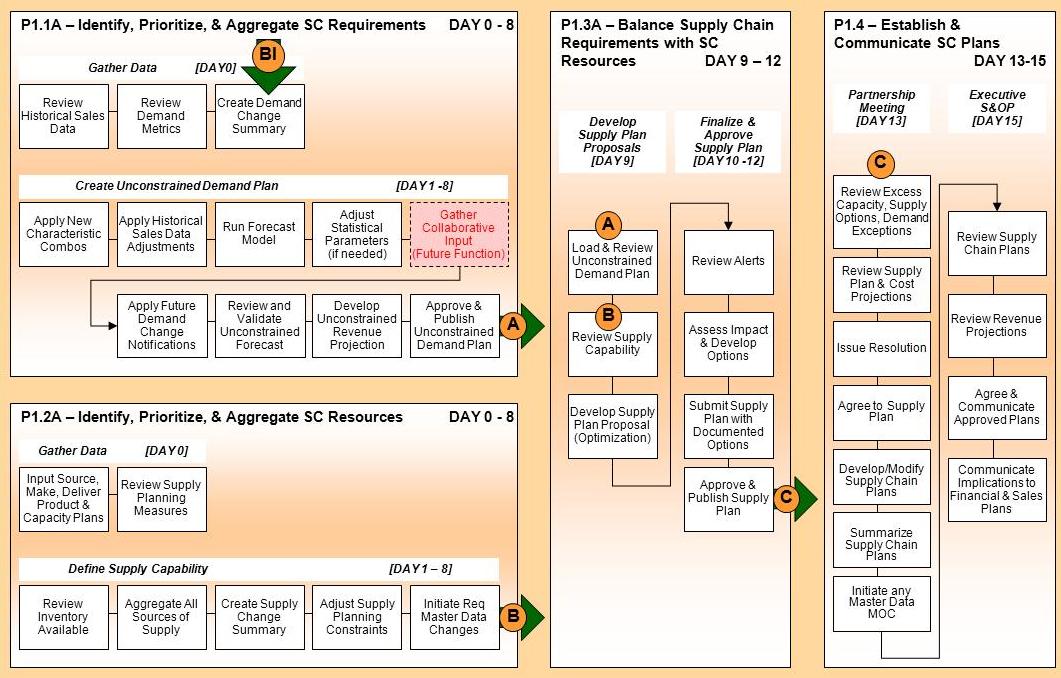



Sap Scm Planning Apo Ibp Typical S Op Process In Apo



Dp S Op Using Sap Apo At Pepsico Pdf Supply Chain Supply Chain Management
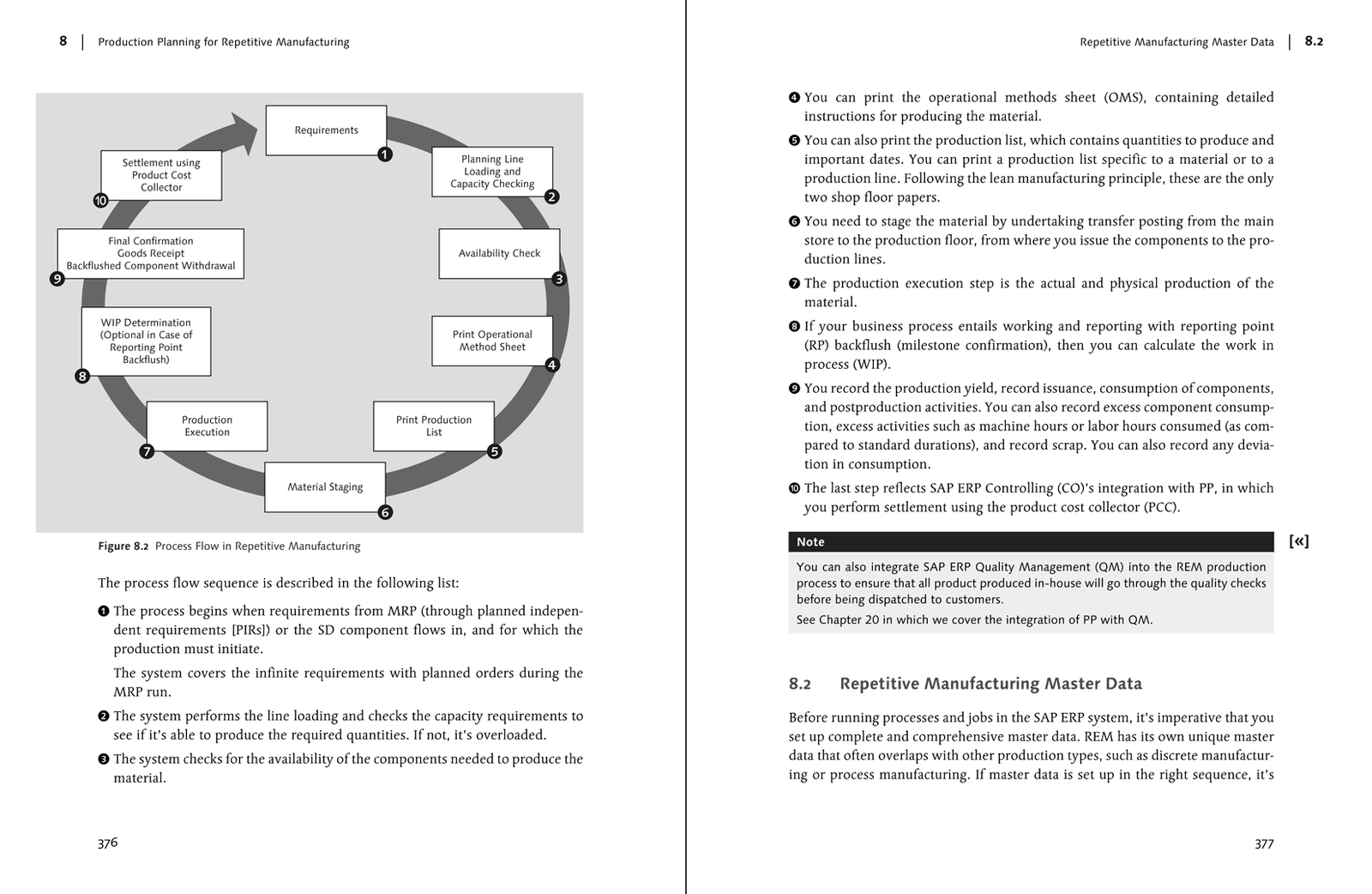



Sap Pp Production Planning And Control Book And E Book By Sap Press
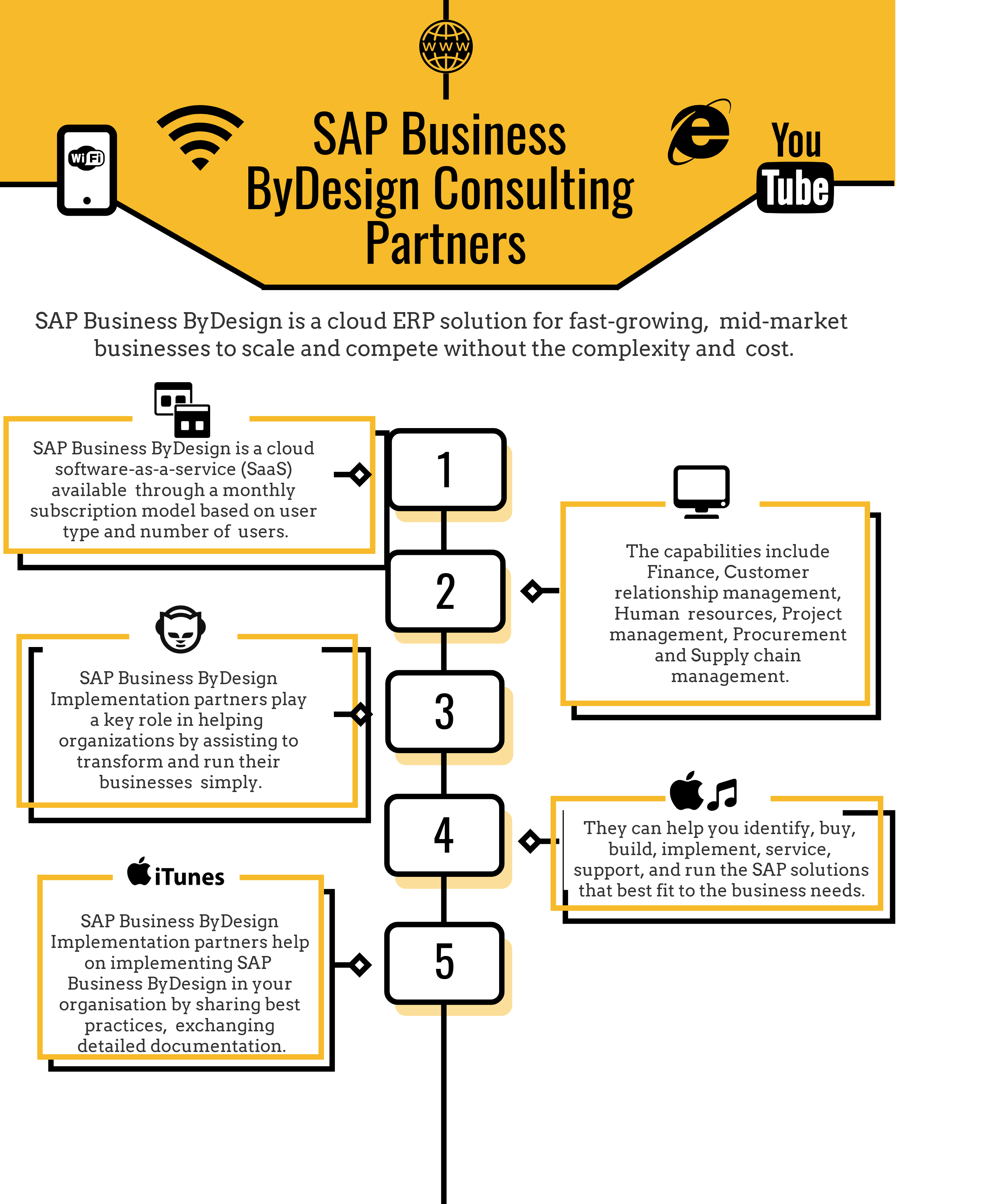



Top 5 Sap Business Bydesign Consulting Partners In 21 Reviews Features Pricing Comparison Pat Research B2b Reviews Buying Guides Best Practices




Sap Sales And Operations Planning Software Product Xsop Pdf Free Download



2
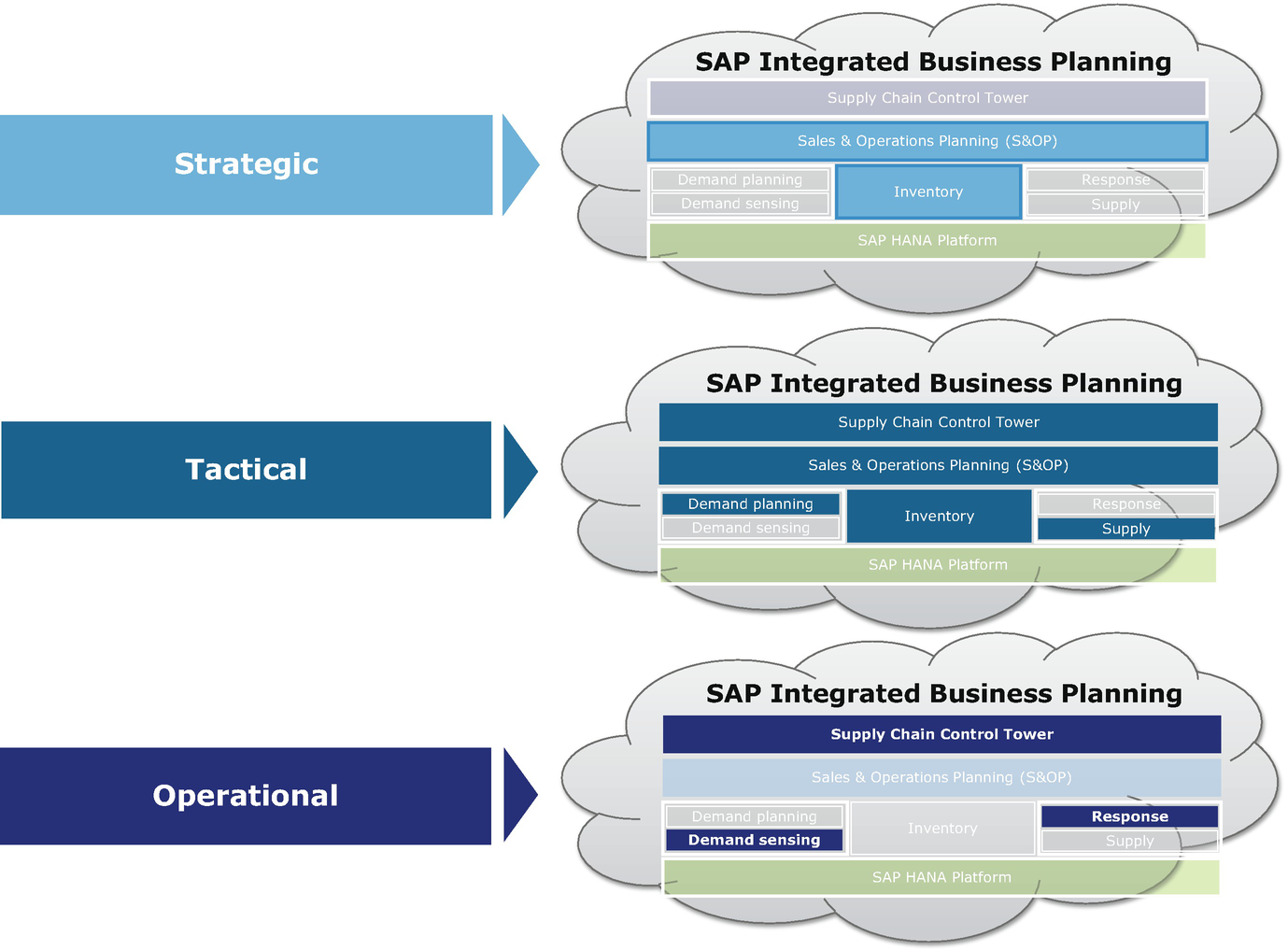



How To Enable Change With Sap Ibp Technology Springerlink




Starter Pack For Sap Integrated Business Planning Food And Beverage Industry Abeam Consulting Korea
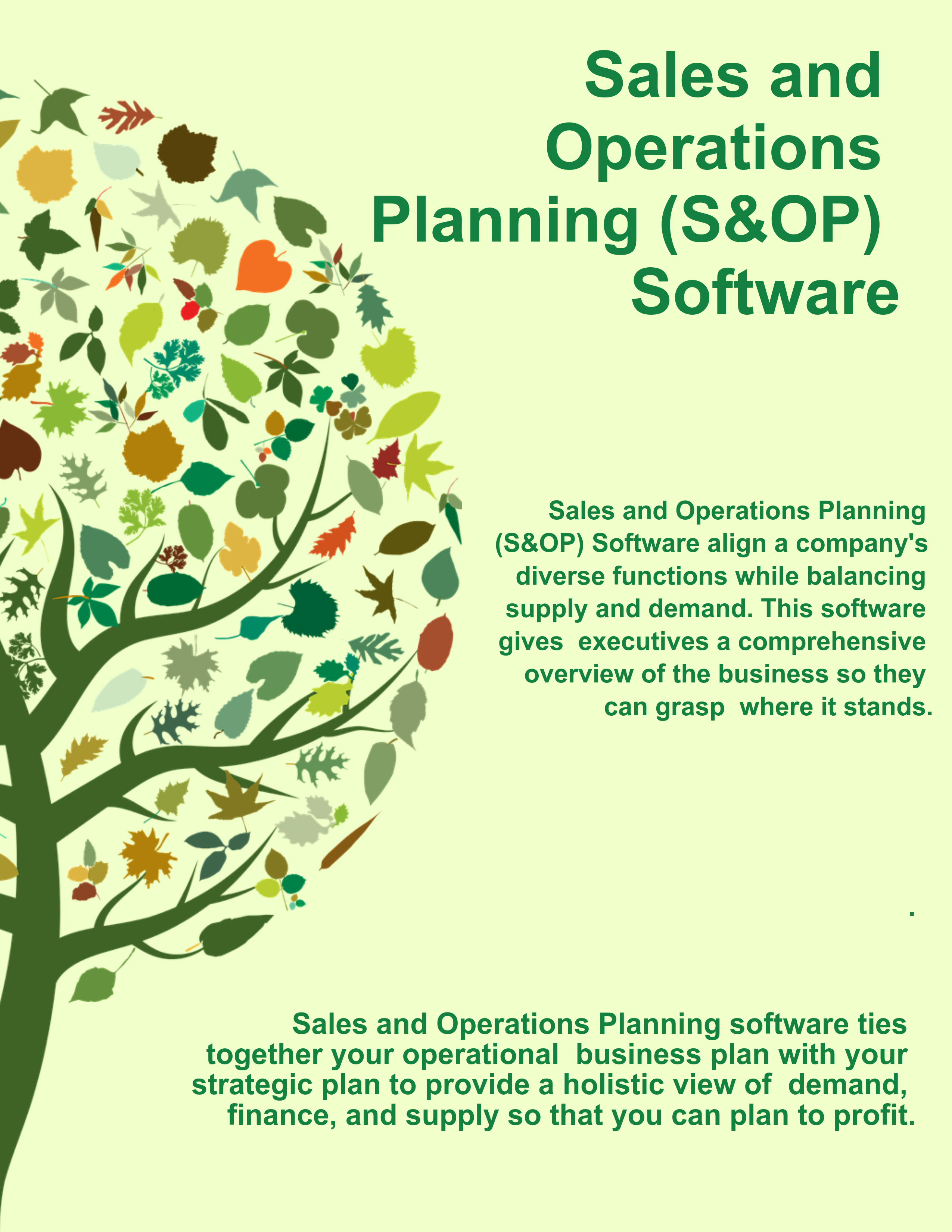



How To Select The Best Sales And Operations Planning S Op Software For Your Business In 21 Reviews Features Pricing Comparison Pat Research B2b Reviews Buying Guides Best Practices




Standard Sop Process Flow Sap Blogs



Production Planning Control Sap Erp Pdf Supernalns




Starter Pack For Sap Integrated Business Planning Food And Beverage Industry Abeam Consulting Korea




Achieve Excellence In Sales And Operations Planning Sapinsider




Sap Integrated Business Planning Ibp Sales And Operations Planning 18 Sap Blogs
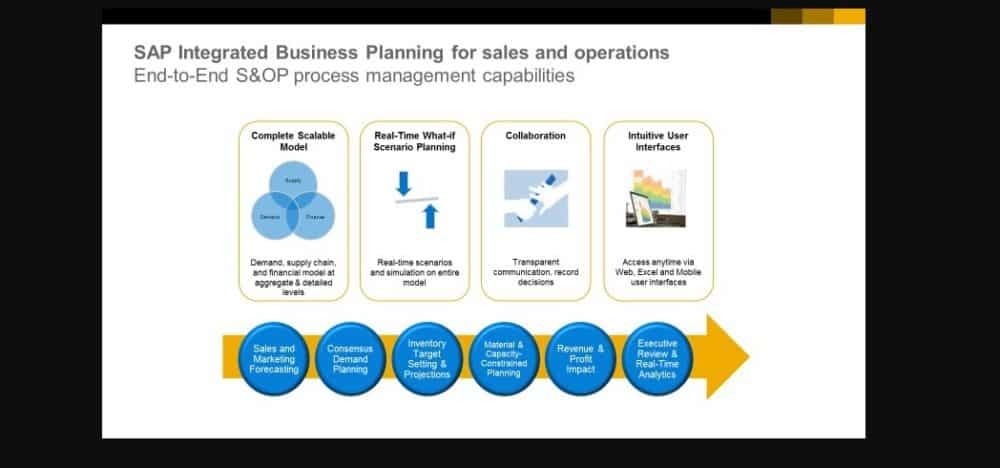



Sap Ibp S Op In 21 Reviews Features Pricing Comparison Pat Research B2b Reviews Buying Guides Best Practices
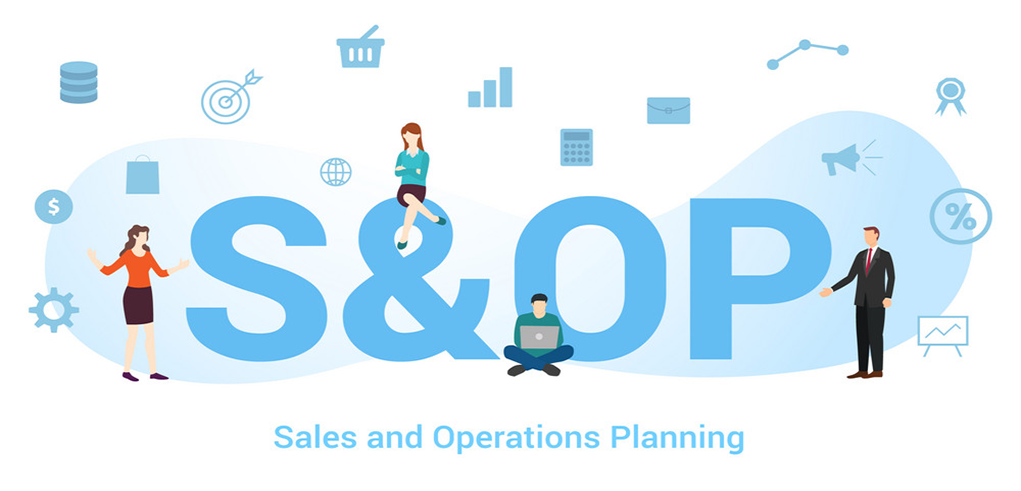



Ultimate Guide To Sales And Operations Planning S Op In 21




Standard Sop Process Flow Sap Blogs




Dissecting Integrated Business Planning Ibp Youtube




Supply Chain Services Reni Analytics Powerful Ai That Powers Business
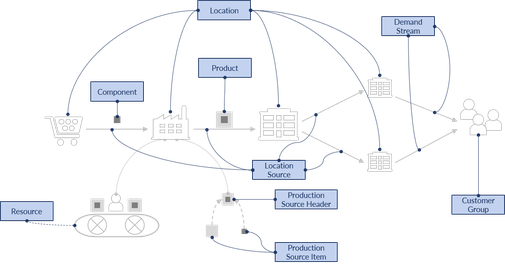



Sap Ibp For Sales Operations Alphachain Consulting



Getting To Grips With Sales And Operational Planning Bloor Research
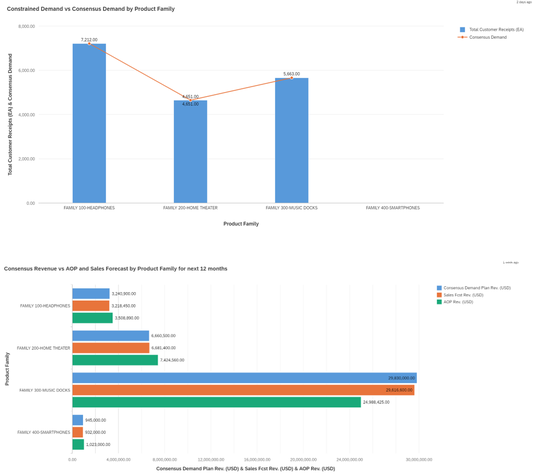



Sap Ibp For Sales Operations Alphachain Consulting




Standard Sop Process Flow Sap Blogs




Standard Sop Process Flow Sap Blogs
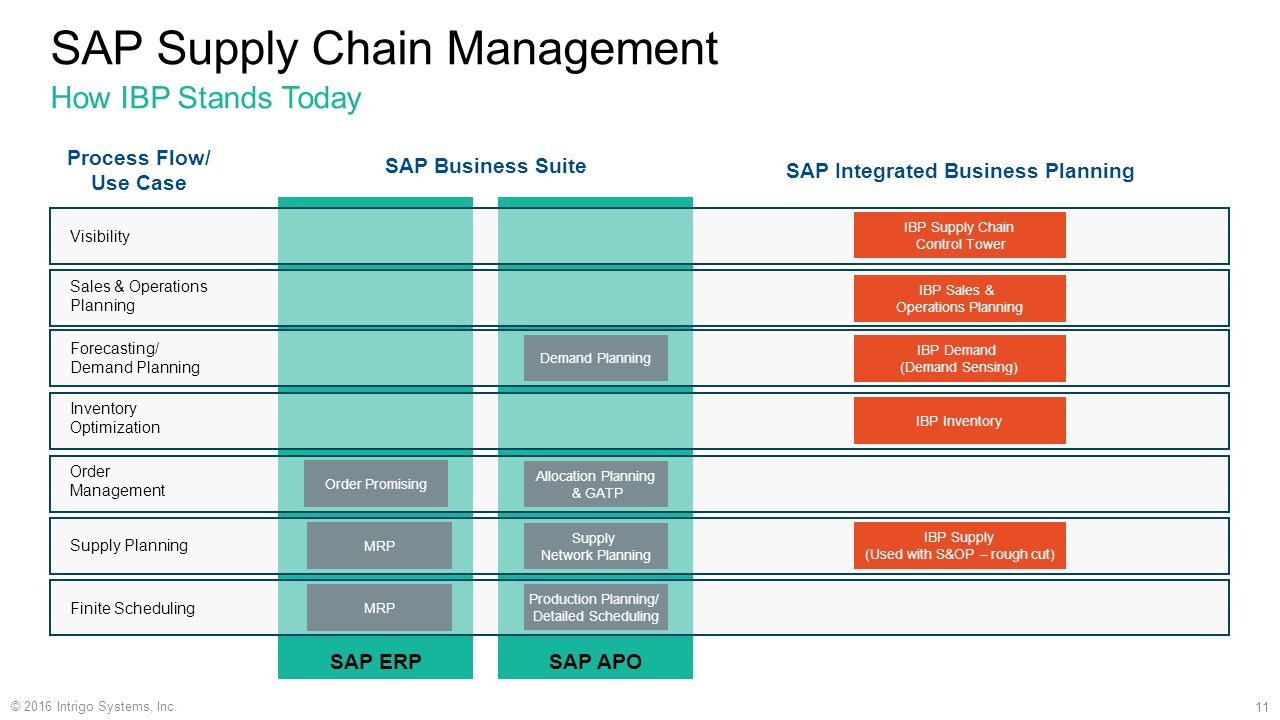



Integrated Business Planning Ppt Video Online Download




Order To Cash Intrigo
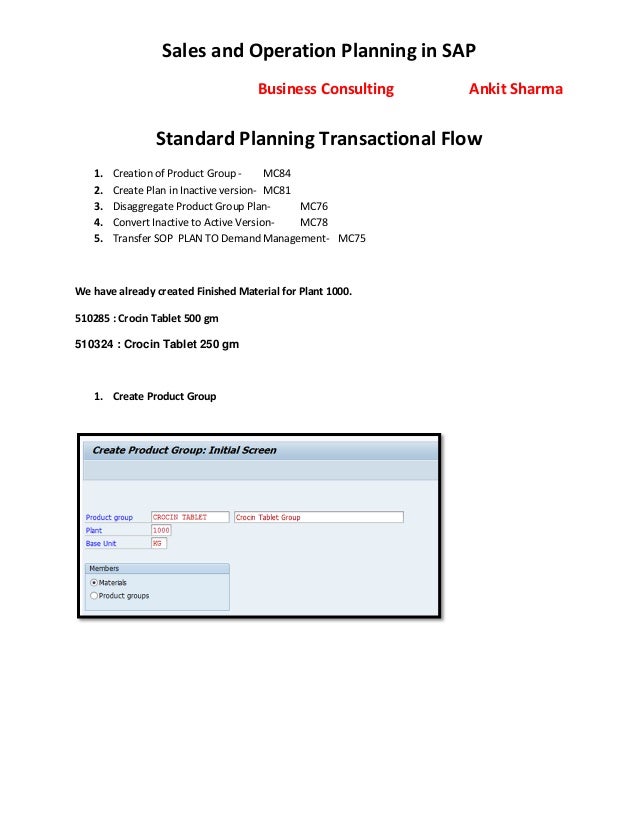



Sales And Operation Planning In Sap




Sap Erp Versus Sap Apo Which Production Planning Functionality Do I Use And How Can I Be Successful Pdf Free Download




Sap Integrated Business Planning Ibp Sales And Operations Planning 18 Sap Blogs
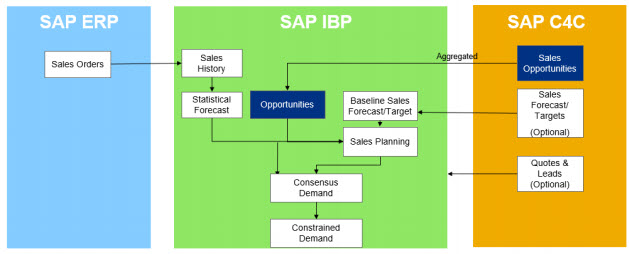



Sap Ibp 1708 Release What S New Gitacloud




Sap Integrated Business Planning Ibp Sales And Operations Planning 18 Sap Blogs



2



2




Achieve Excellence In Sales And Operations Planning Sapinsider
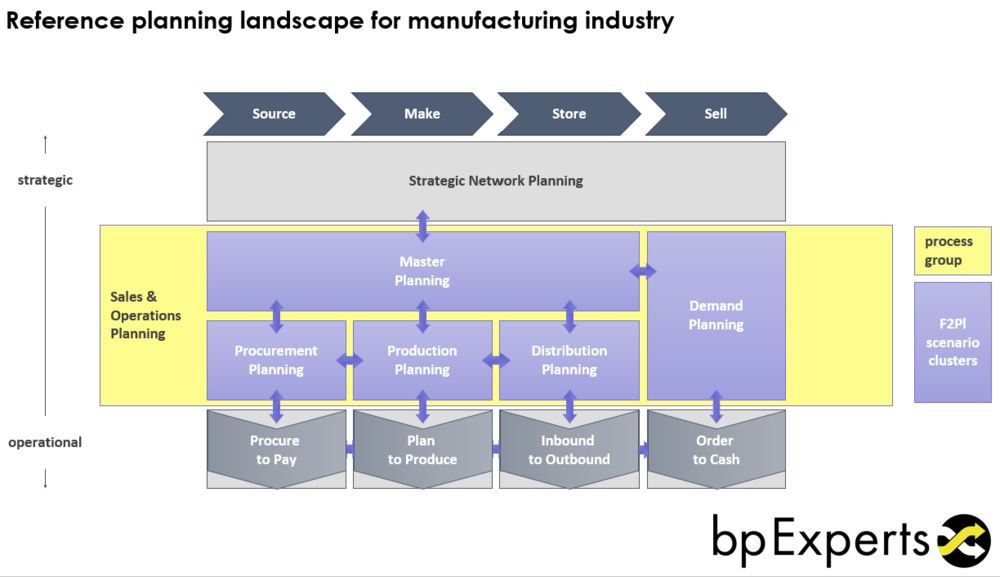



F2pl Bpexperts



1




Dp Vs S Op Process Flow




Dp S Op Using Sap Apo At Pepsico
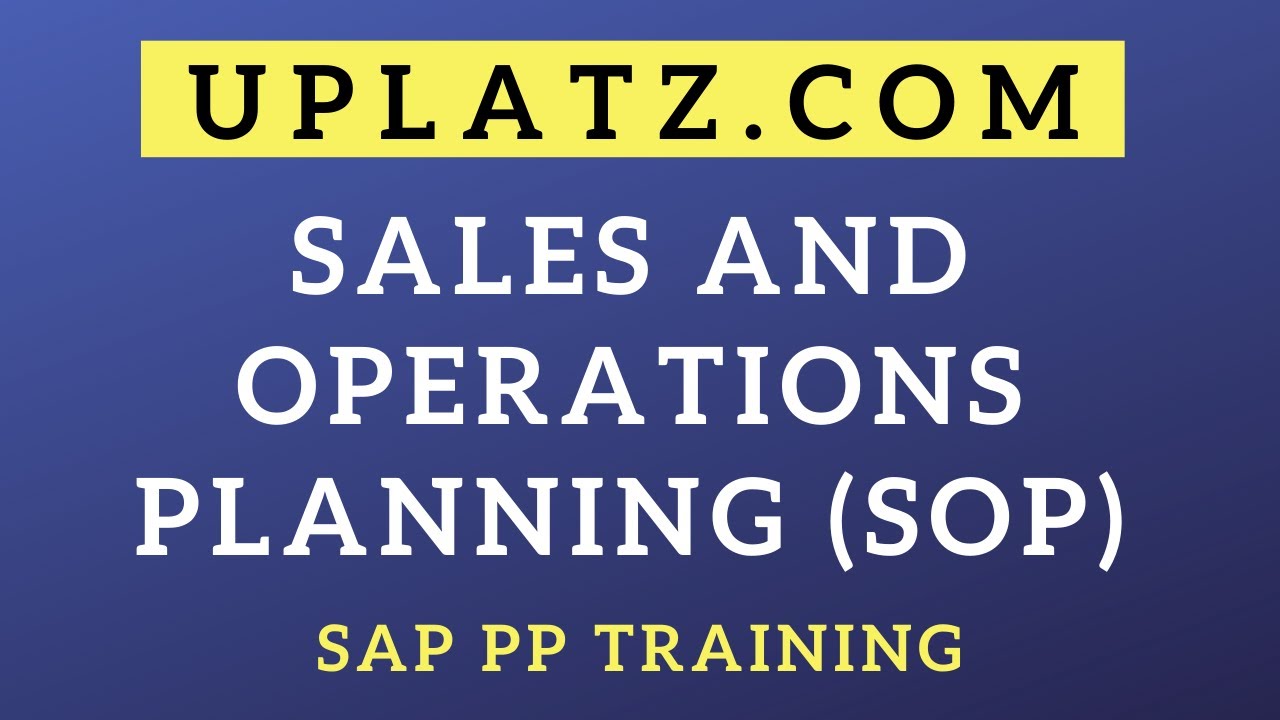



Sales And Operations Planning Sop Sap Pp Training Sap Pp Tutorial Sap Pp Course Uplatz Youtube
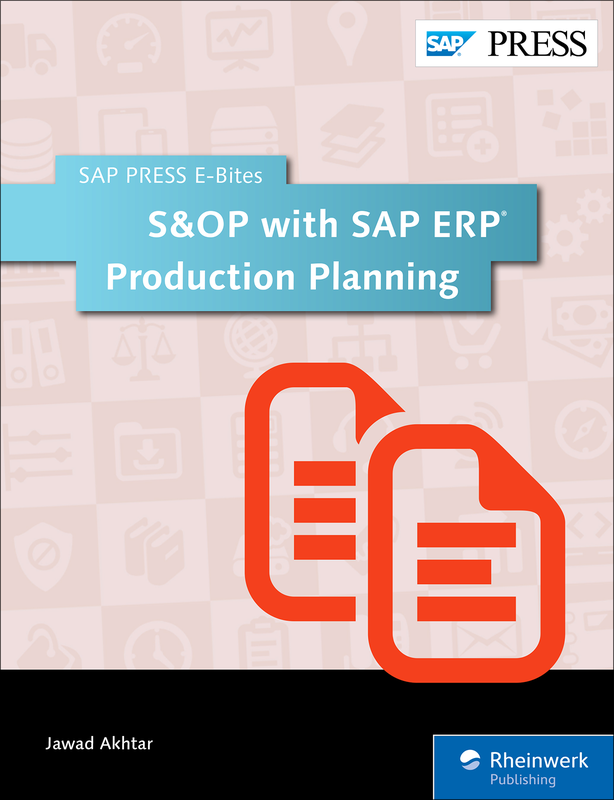



Sap Pp Sap Production Planning S Op How To Guide By Sap Press




Sap Best Practices For Sap Integrated Business Planning 1902 Sap Blogs




Sap Integrated Business Planning Ibp Sales And Operations Planning 18 Sap Blogs




How To Improve Sales And Operations Planning With Ready To Run Solutions For Sap Ibp




Options For Implementing Sap Integrated Business Planning For Demand




Sap Mes Intrigo
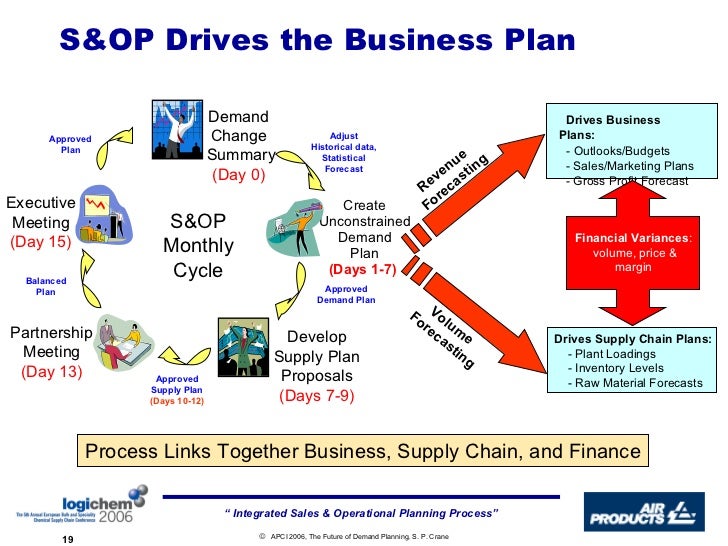



Implementing An Integrated Sales And Operations Planning Process
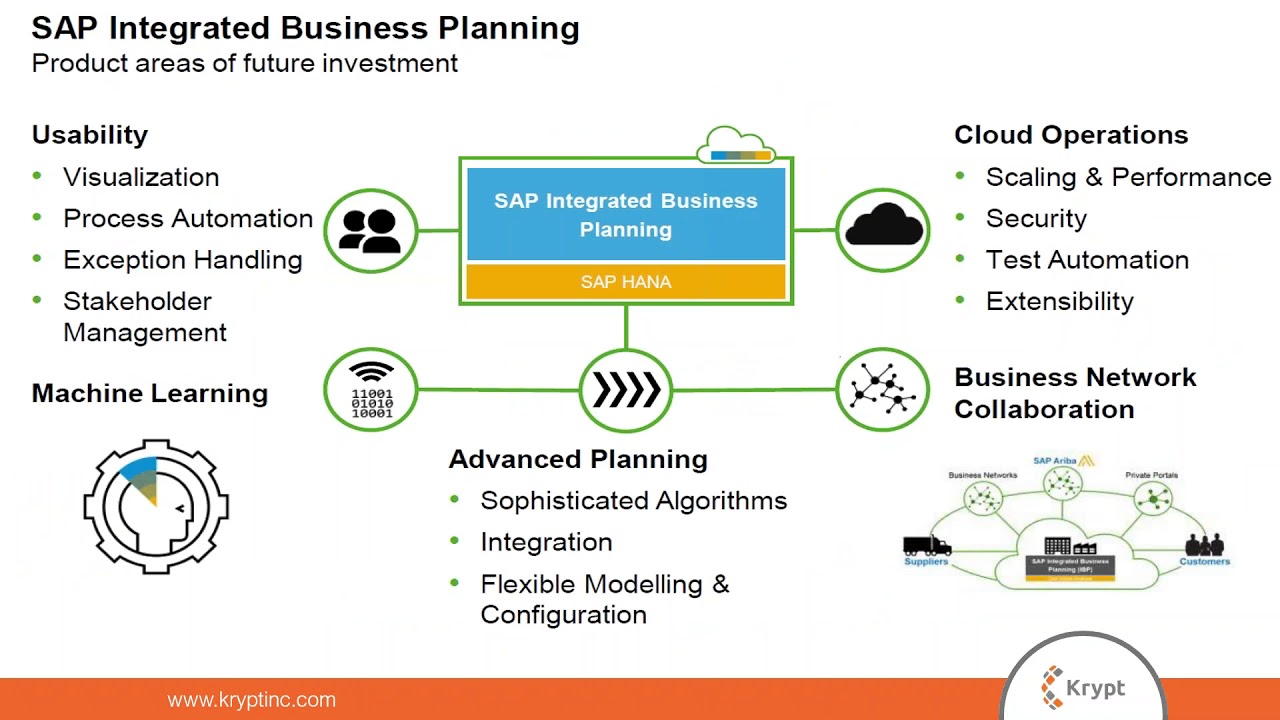



Introducing Sap Ibp S Op Processes Webinar Youtube




Sap Sales And Operations Planning Software Product Xsop Pdf Free Download
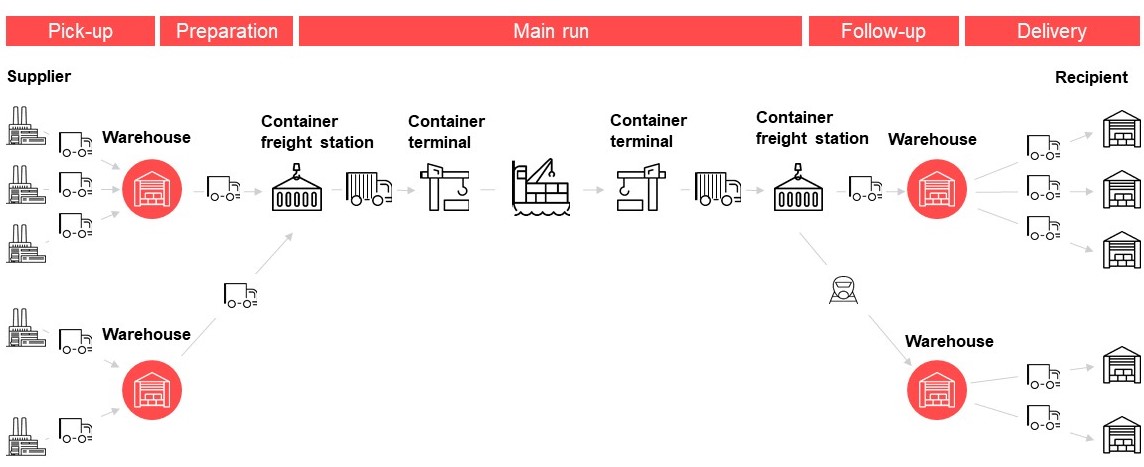



Become An Intelligent Enterprise With Sap Services Valantic
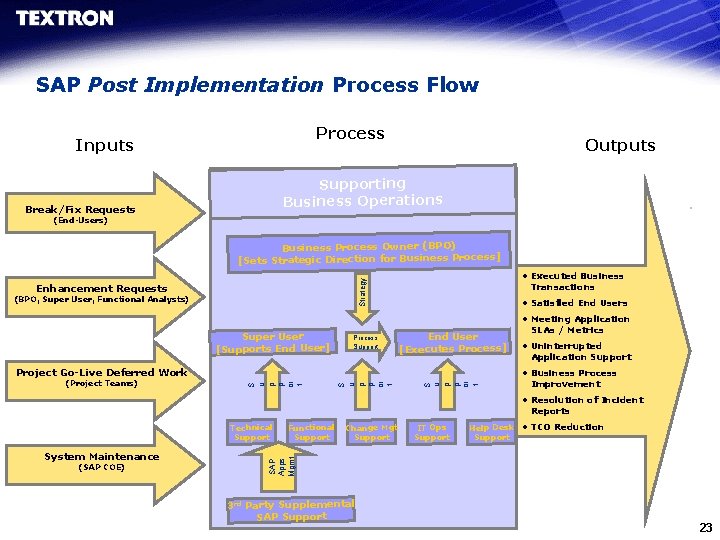



Creating And Running A Sap Support Organization Bryant




Scm Apo Supply Chain Planning Process Overview Blueprint




What Is S Op Sales And Operations Planning Sap Insights




Standard Sop Process Flow Sap Blogs




Pdf A Case Method For Sales And Operations Planning A Learning Experience From Germany



2
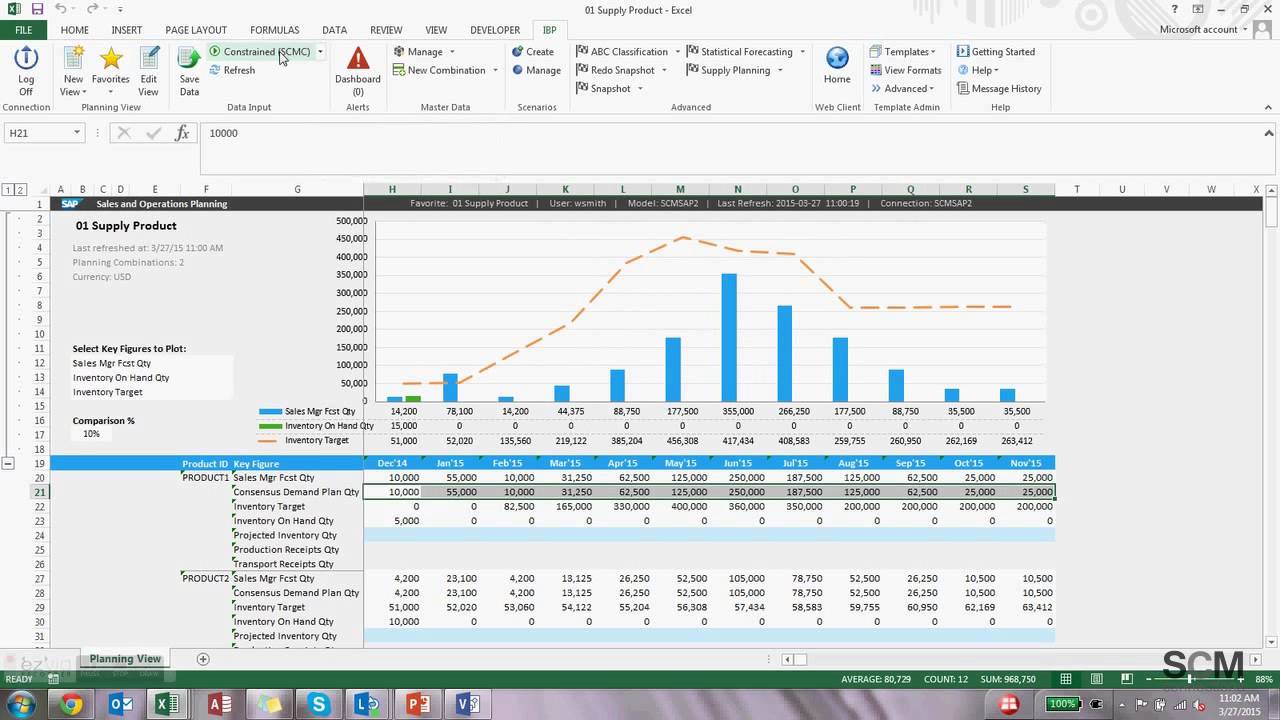



Sap Integrated Business Planning




Sales Operations Planning S Op Sap Library Sales Operations Planning S Op
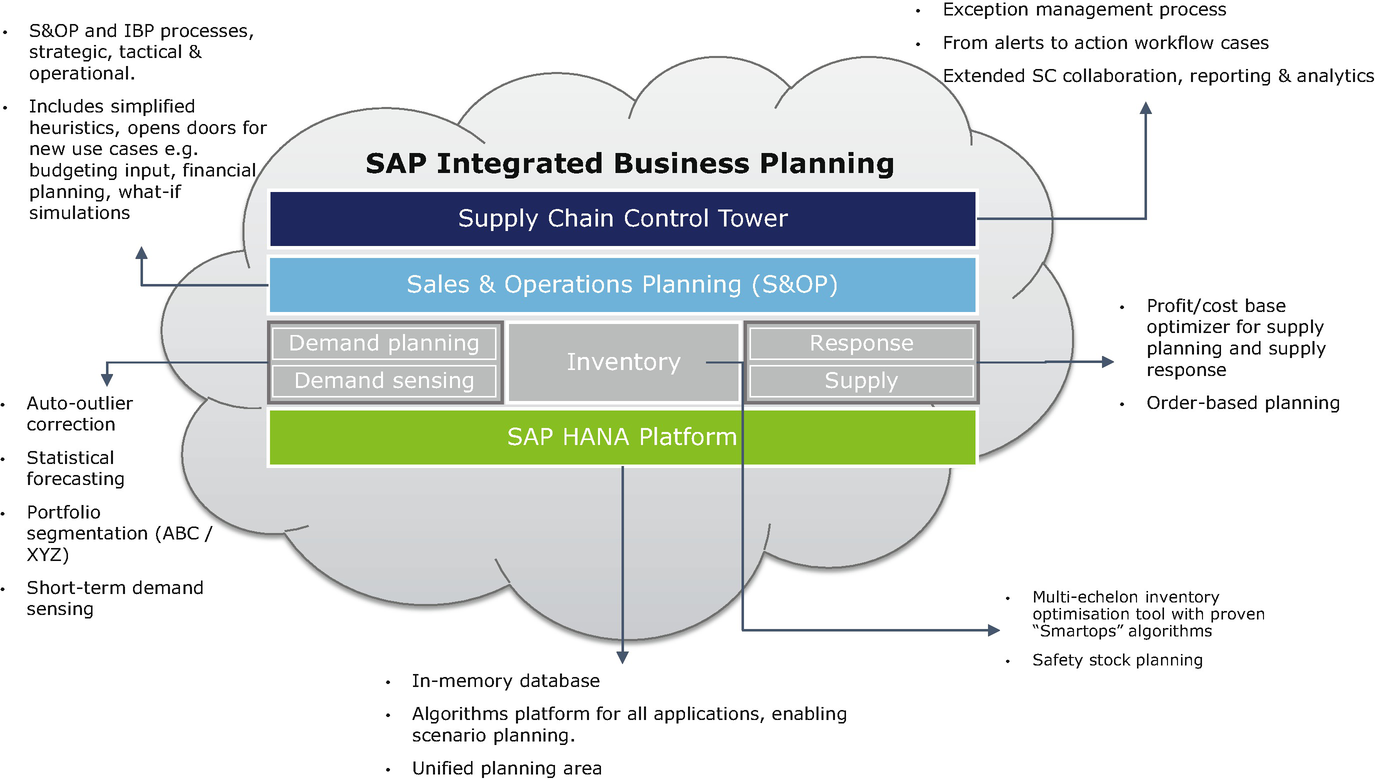



How To Enable Change With Sap Ibp Technology Springerlink
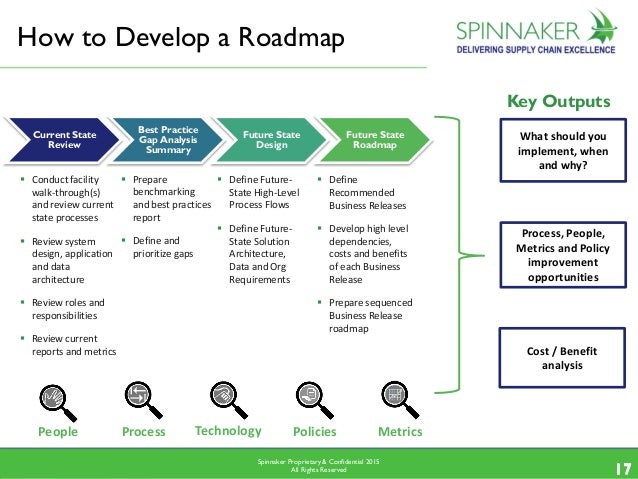



Building A Roadmap To Adopt Sap Integrated Business Planning Ibp




Sales And Operations Planning S Op Is All About Balancing Supply And Demand Implement Consulting Group




Pin On Erp Training Concepts




Process Flow For Sales Orders Sap Documentation
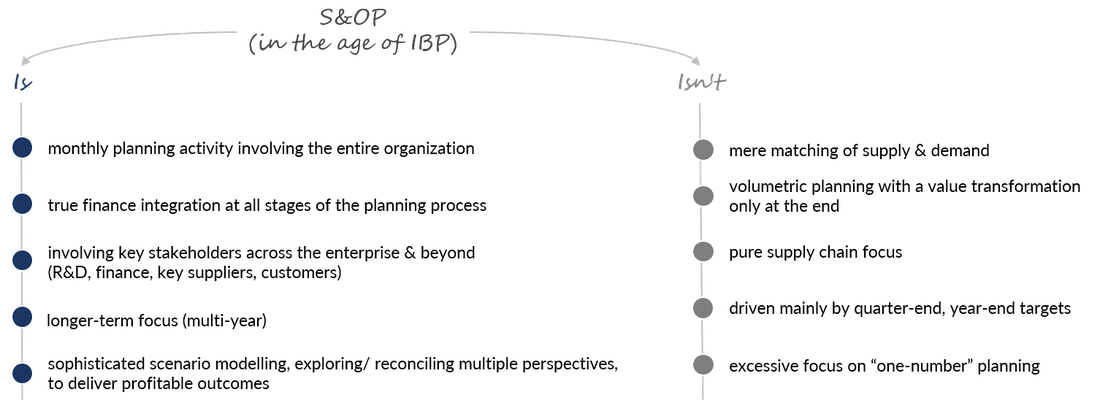



Sap Ibp For Sales Operations Alphachain Consulting
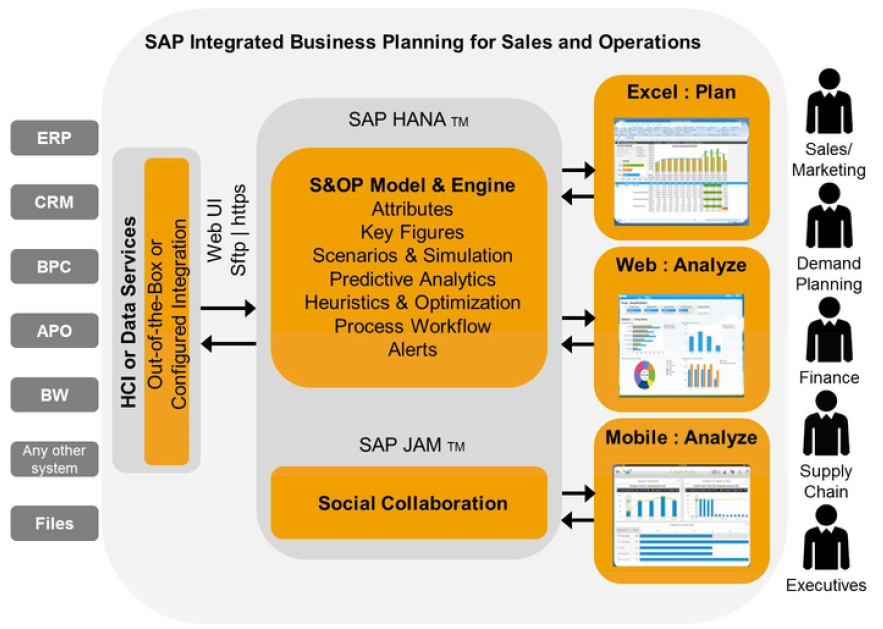



Sap Ibp Gitacloud



1



2



1
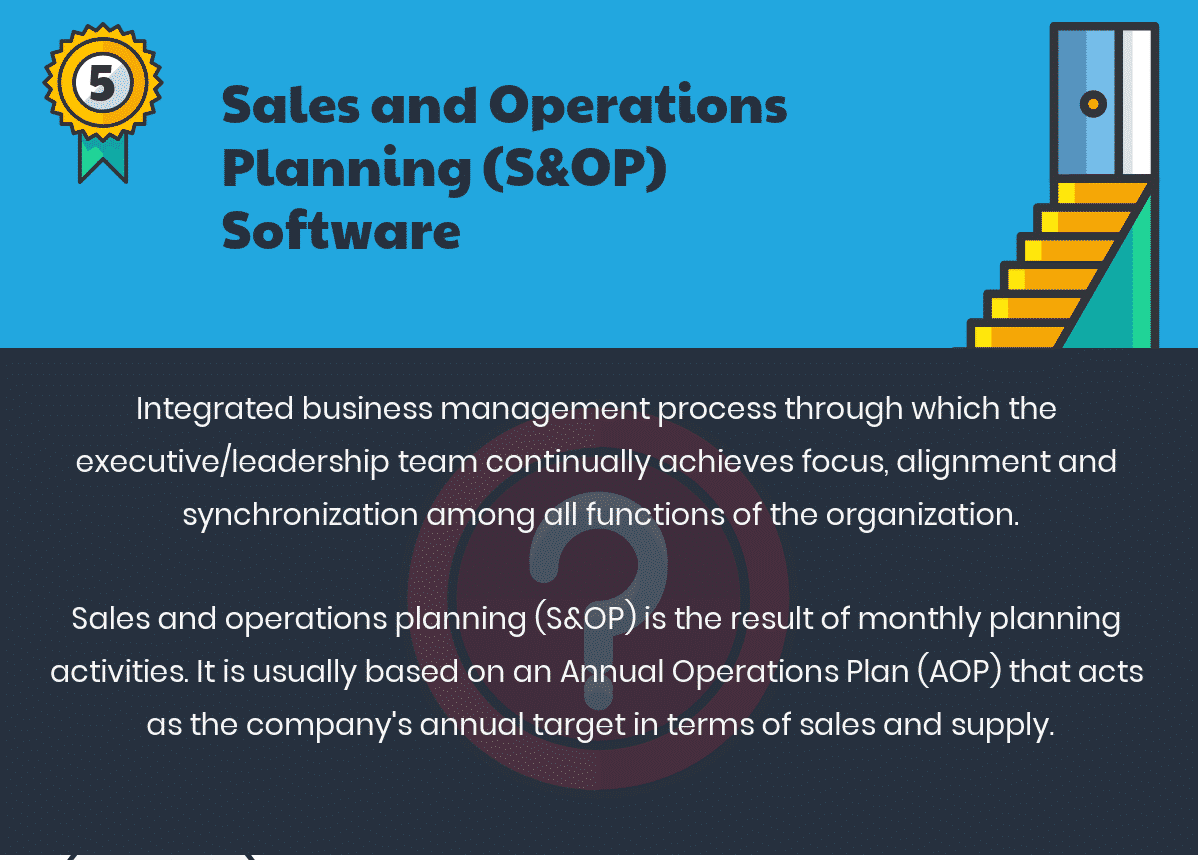



Top 11 Sales And Operations Planning S Op Software In 21 Reviews Features Pricing Comparison Pat Research B2b Reviews Buying Guides Best Practices




Achieve Excellence In Sales And Operations Planning Sapinsider
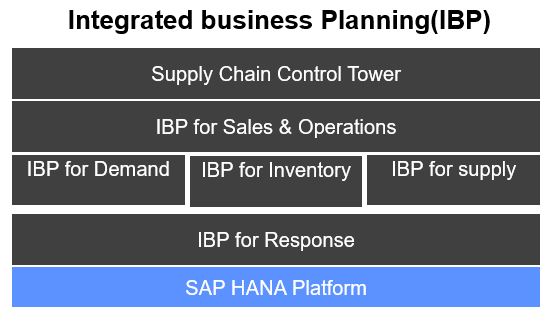



Sap Ibp Demand Planning Sap Integrated Business Planning Training




Sap Ibp Sales Operations Planning



2
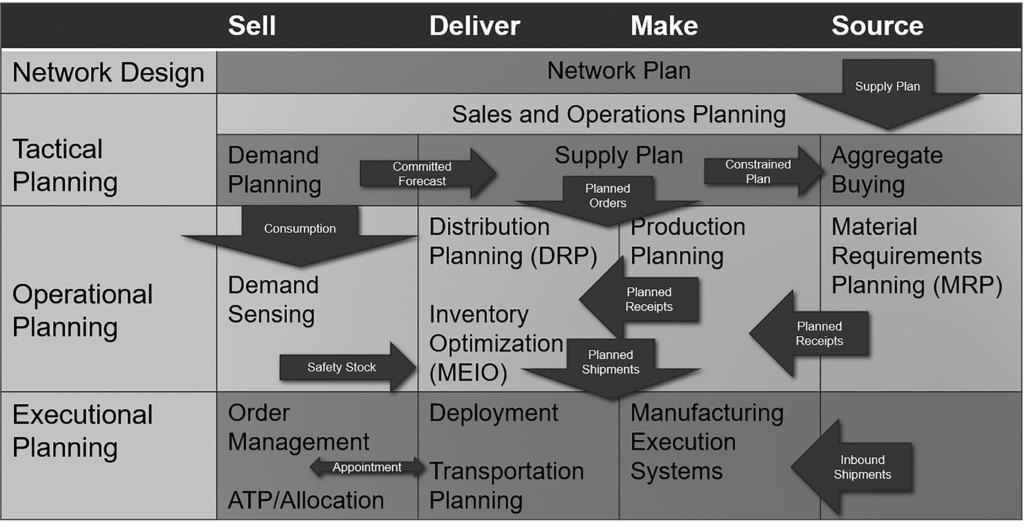



Is S Op Excellence Slip Slidin Away Supply Chain Shaman



A Comprehensive Overview Of Sales And Operations Planning S Op
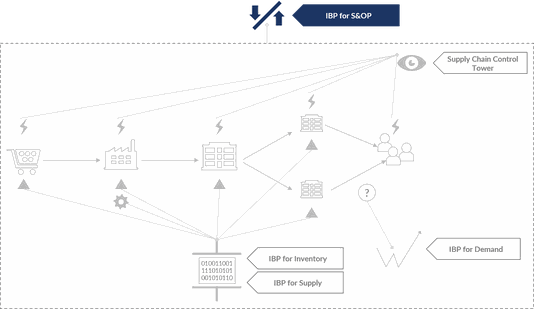



Sap Ibp For Sales Operations Alphachain Consulting




Sap Mm Purchasing Flow In A Nutshell Sap Blogs




Standard Sop Process Flow Sap Blogs




A Global Cpg Major Transformed Its Procurement Planning Process Through Sap Integrated Business Planning Thoucentric Management Consulting




Pdf Sales And Operations Planning S Op An Overview




Standard Sop Process Flow Sap Blogs
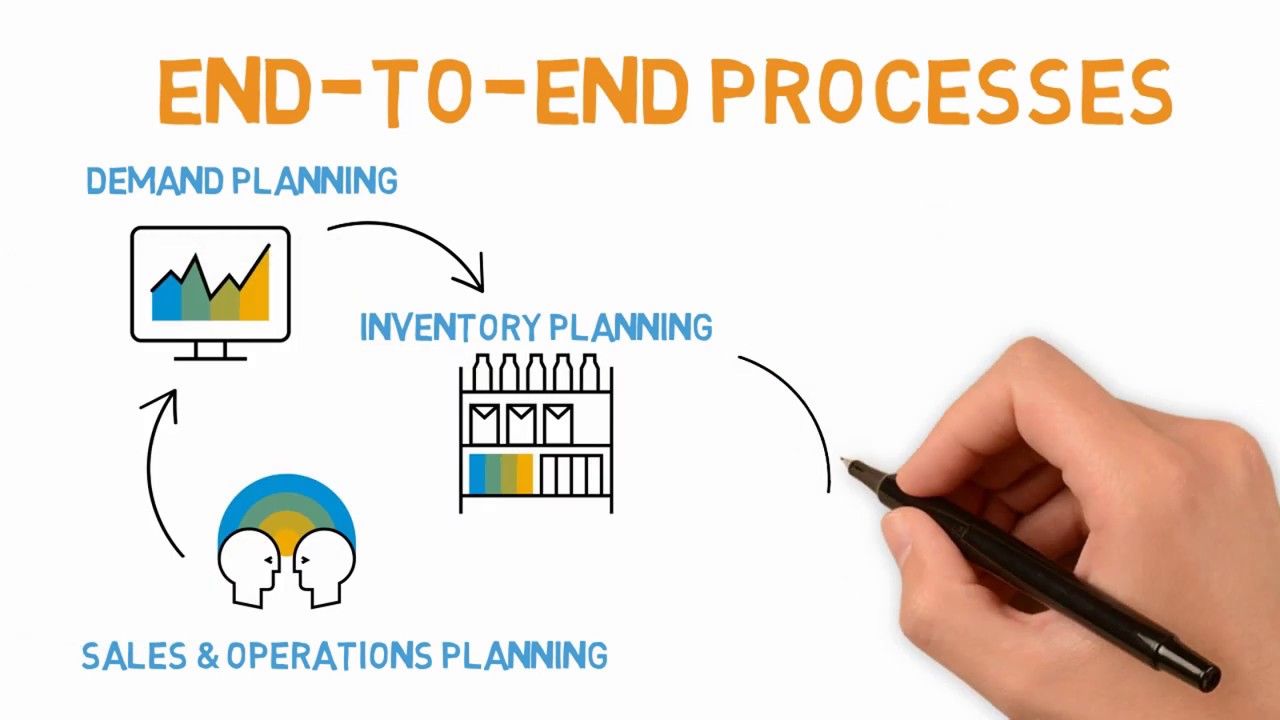



Take Off With Sap Best Practices For Sap Integrated Business Planning Youtube




Standard Sop Process Flow Sap Blogs
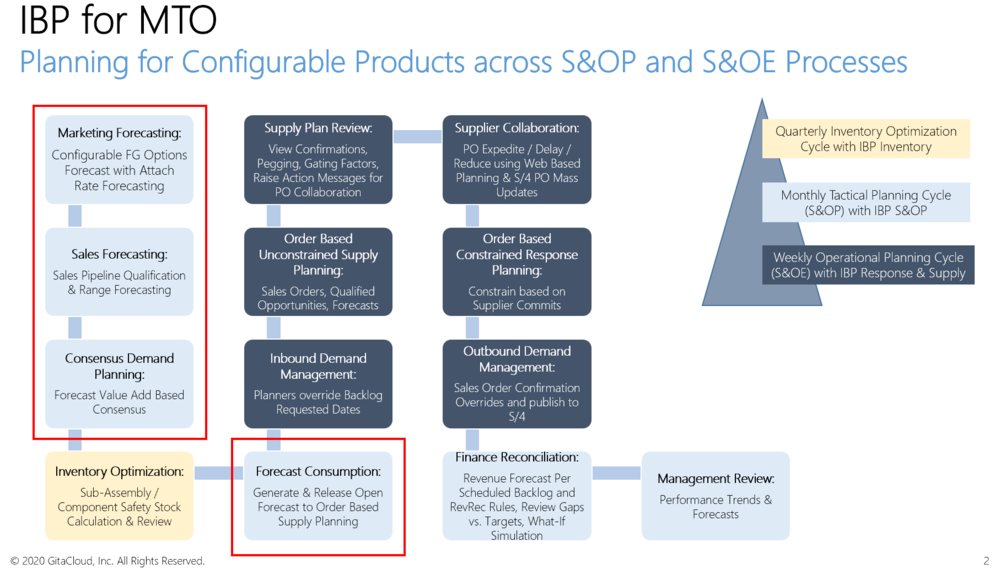



Configurable Products Planning How Make To Order Mto Industries Plan In The Real World Gitacloud




Pdf Design Of A Sales And Operations Planning S Op Process Case Study
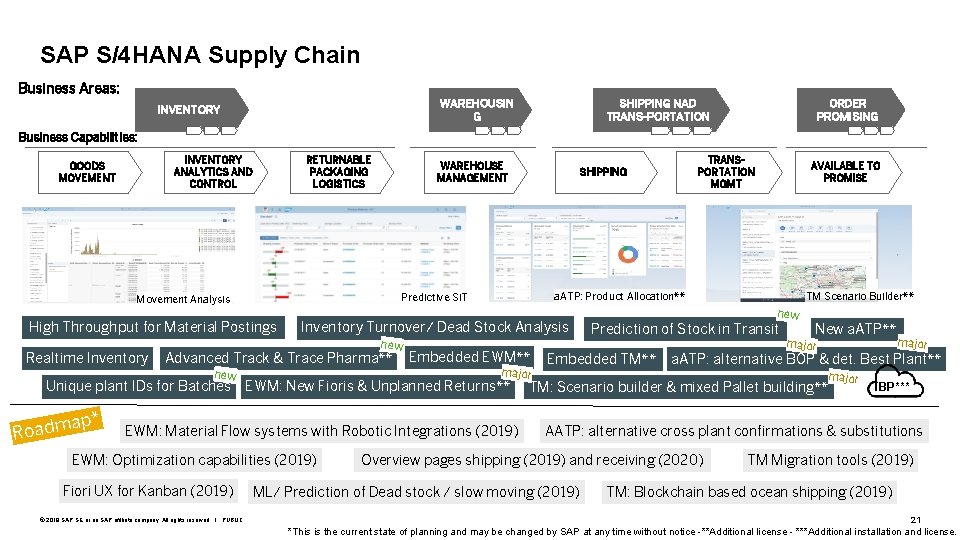



Introduction And Overview The Core Of The Intelligent




Achieve Excellence In Sales And Operations Planning Sapinsider




Working Together Collaboration In Sap Ibp For Sales And Operations Sap Blogs
0 件のコメント:
コメントを投稿